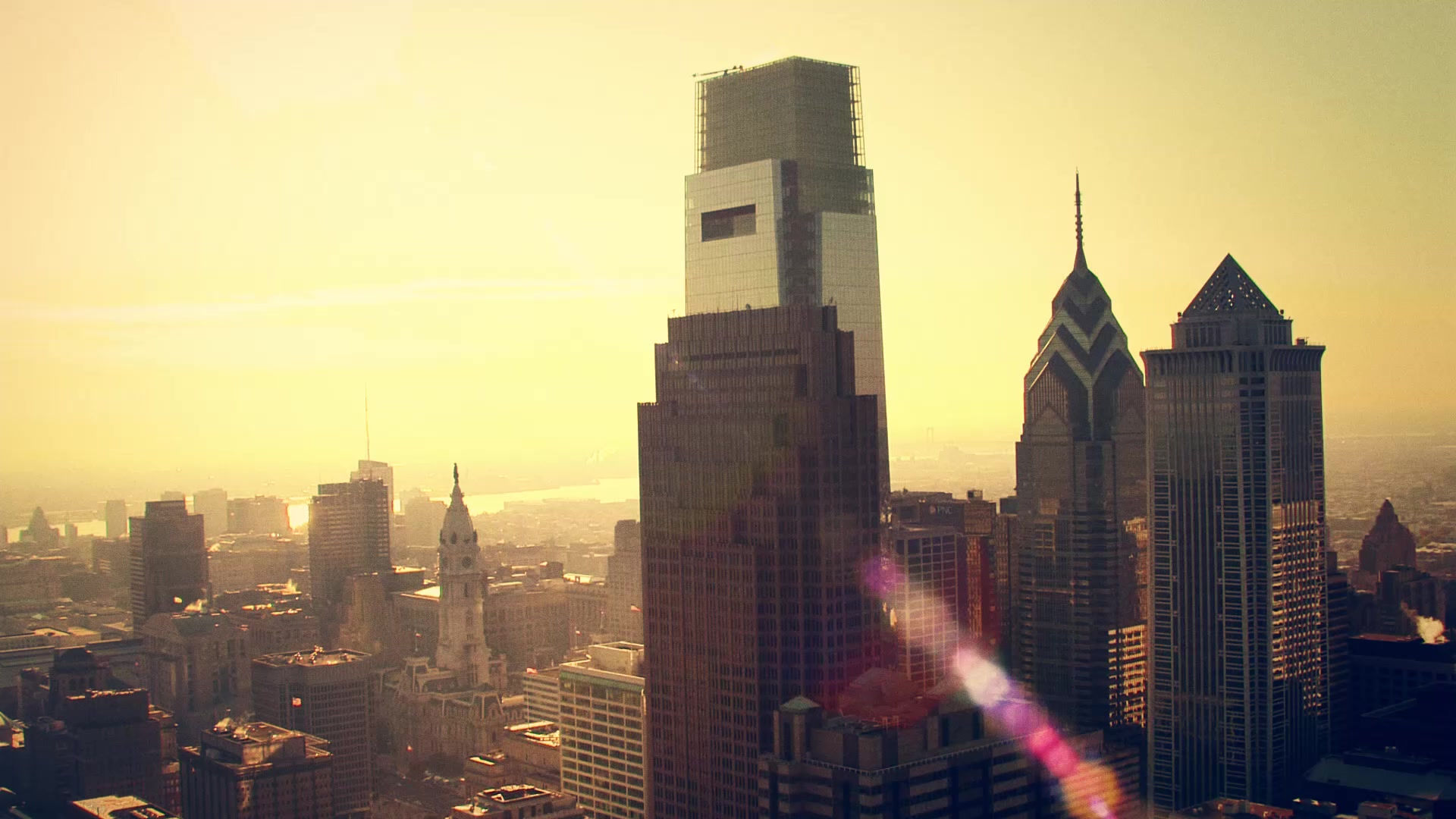

2025 Award Winners and Nominees
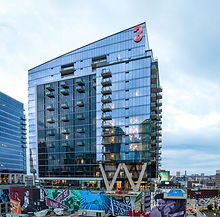
Project Name
Three Light Tower
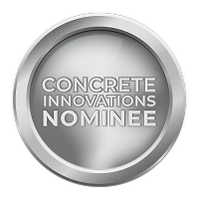
Description
Completed and occupied on 9/28/23, The Cordish Companies’ Three Light Tower project included the construction of a 25-floor, 508,000 SF apartment complex and parking garage. The “Double Vee Columns” on the main amenity floor were a highlight of the design and fabrication process, developed in collaboration with HCM (architect), McLaren Structural Engineers (structural engineering), JEDunn (GC & self-perform group), and Talon Aggregates (mix provider & ARMCA Member).
The “Double Vee Columns” were a mini-project within the larger tower, serving a structural role for the floors above. The first 11 months involved mix design submissions, formwork engineering, procurement, and fabrication, culminating in a 28-hour uninterrupted concrete pour sequence.
Standing over 35’ tall and 60’ wide, the Double Vee featured complex geometry, tapering at the top and cantilevering in multiple directions. As both a structural and exposed element, precision was crucial in its execution. The site’s tight space added further complexity, as there was no room for mapping out or assembling the formwork on-site.
The pre-build team utilized 3D modeling and CNC equipment to design and build a complex formwork system that could be easily transported in four separate pieces, one for each arm of the Double Vee. Formwork construction had to be highly precise, given the varying angles of each piece. Once assembled on-site, the forms allowed for rebar installation before concrete pouring. After curing, the forms were carefully disassembled for removal.
The Double Vee's "W" shape presented a challenge in that vibration couldn’t be used to consolidate the mix. Any vibrators would get stuck along the reinforcing steel on the sloped surface. To address this, innovative methods were employed to maintain structural integrity.
The formwork was designed by JEDunn’s in-house fabrication team and had to be precisely aligned with the 8th-floor bearing points and the not-yet-formed 11th floor. The use of self-consolidating concrete optimized the column’s aesthetic and minimized the need for retouching. In the end, only light sanding was needed to finish the surface, preserving the architect’s original vision without defects.
This project demonstrates the potential of concrete in modern architecture, pushing the limits of design and construction while prioritizing sustainability and efficiency.
Evidence
Talon Aggregates provided all the concrete mixes for the tower’s construction, from slab on grade, mass concrete pour of the elevator base, columns and decks as well as the double vee column’s special 8000psi self-consolidating mix.
JEDunn and Talon took the challenges represented by the design element seriously in a number of ways; the tall, exposed concrete in a unique geometry hanging off the side of a structure under construction, testing the placement of the specialty mix on a few columns of the garage a level below, verifying the feasibility of craning nearly 40’ long shop-built formwork into place, all the while supporting the forms, the reinforcing and of course the uncured mix until the forms could be removed. All the early planning and practice and mock-ups for this type of design-yet-structural element really paid off, once stripped, the concrete needed only a light rubbing.
Images

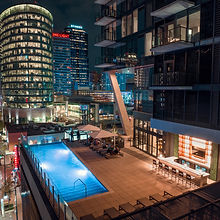



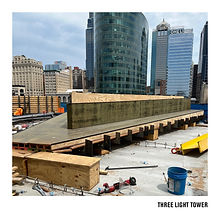


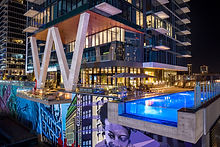


