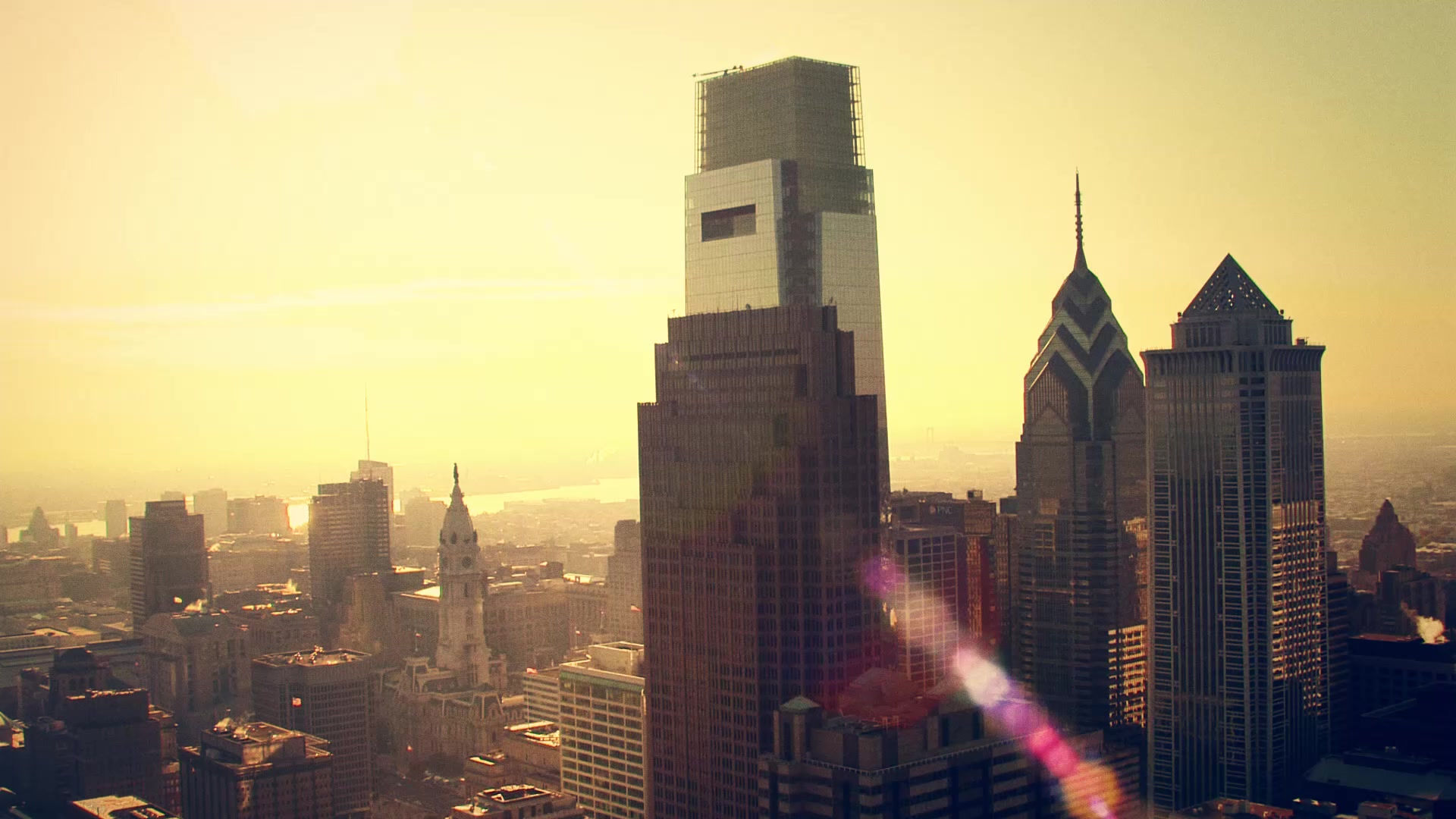

2025 Award Winners and Nominees
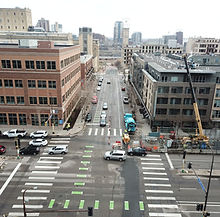
Project Name
Central City Parallel Tunnel

Description
Seated on the banks of the Mississippi and Minnesota Rivers; Minneapolis, Minnesota is home to a bustling population of more than 425,000 citizens. It is the largest city in the state and is supported through extensive underground infrastructure – most of which is decades old. The most pressing concern with this important and often overlooked infrastructure is the deterioration of the stormwater tunnels beneath the city. Originally built in 1939 and 1940, the stormwater tunnels transport water into the Mississippi River during rain events. A rapid growth in population over the last 80 years and a 30% increase in rainfall per hour over the last 50 years necessitates repair and modification of the current tunnel system to accommodate the increased water flow. The strain of excessive amounts of water caused cracking and deterioration of the concrete tunnels, resulting in yearly repair costs close to $600,000 annually.
In 2021, the City of Minneapolis Public Works Department approved a $60 million overhaul of the stormwater tunnel system and contracted CNA Consulting Engineers to design a new stormwater tunnel system would last 100 years and would be twice the size of the current system for moving stormwater from downtown Minneapolis to the Mississippi River. The project known as the Central City Parallel Storm Tunnel Project was a 3-year project, completed in the Summer of 2024.
The contractor, PCiRoads, was tasked with rehabilitating 800 feet of tunneling and adding an additional 3,600 feet of new tunneling 80 feet below the surface of Minneapolis. The initial challenge was finding equipment small enough but resilient enough to be lowered via crane, down into the existing tunnel. The constrained site and available access continued to be a major challenge throughout the project impacting concrete mixture design and placement techniques.
Cemstone Products Company is the NRMCA member company that designed and supplied 23,000 yards of highly technical concrete for this project. Cemstone’s use of supplementary cementitious materials in the concrete was of utmost importance to minimize the environmental footprint and meet the performance-based specifications. Cemstone’s task was to design and supply concrete mixtures meeting the unique challenges of the project, which included maximum shrinkage requirements for mixtures that would be pumped up to 1,200 feet.
Evidence
Cemstone Products Company, an NRMCA member company, was responsible for designing, testing, and supplying 23,000 cubic yards of concrete for this project. The concrete mixtures became extremely technical due to the project requirements while having limited site access for delivering and placing the concrete into the tunnel system.
Cemstone utilized Supplementary Cementitious Materials (SCM’s) to achieve the required life cycle of the structure and to minimize the environmental impact of the concrete. A key project requirement was to limit water intrusion into the tunnels by minimizing cracking. The project’s performance-based specification required low shrinkage concrete with a maximum allowable shrinkage of 0.03% when tested in accordance with ASTM C157 (modified to a 7-day wet curing period).
The challenge of designing a concrete mixture that would pump 1,200 feet and achieve the low shrinkage requirement was unique. Long distance pumping and low shrinkage concrete conflict with each other due to the differing paste content demands. Cemstone Engineering Services was able to collaborate with Cemstone Placing to design a mixture that achieved both requirements. It was determined that a Shrinkage Reducing Admixture (SRA) was needed to ensure the shrinkage requirement was met. The resulting mixture achieved a shrinkage of 0.013% and successfully pumped the required distance.
The SRA, accompanied by the concrete being specified as air-entrained, presented an additional challenge. SRA’s typically make it difficult to control the air content during production and placement. Cemstone’s Operations and QC personnel developed a quality control plan to address this challenge. The QC plan was successful throughout the 28-month project duration.
The GWP savings of the concrete for the project was over 2.1 million kg CO2-eq. The relevant details of the two main mixtures are below.
5000 psi Structural Concrete:
• 17,815 cy
• 40% Cement Replacement
• GWP – 220 kg CO2-eq/cy (22.7% reduction)
• GWP Savings 1.15 million kg CO2-eq
o Compared to North Central Regional Average (NRMCA Industry Wide LCA Project Report – V 3.2)
3000 psi Neat Cementitious Flowable Fill:
• 2,208 cy
• 67% Cement Replacement
• GWP 372 kg CO2-eq/cy (55.4% reduction)
• GWP Savings 1.02 million kg CO2-eq
o Compared to a typical mix for the application, there is not an equivalent mixture in the North Central Regional Average (NRMCA Industry Wide LCA Project Report – V 3.2)
Images
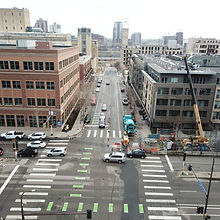

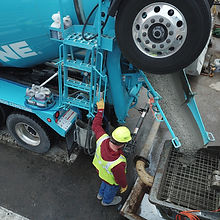






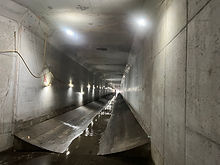

