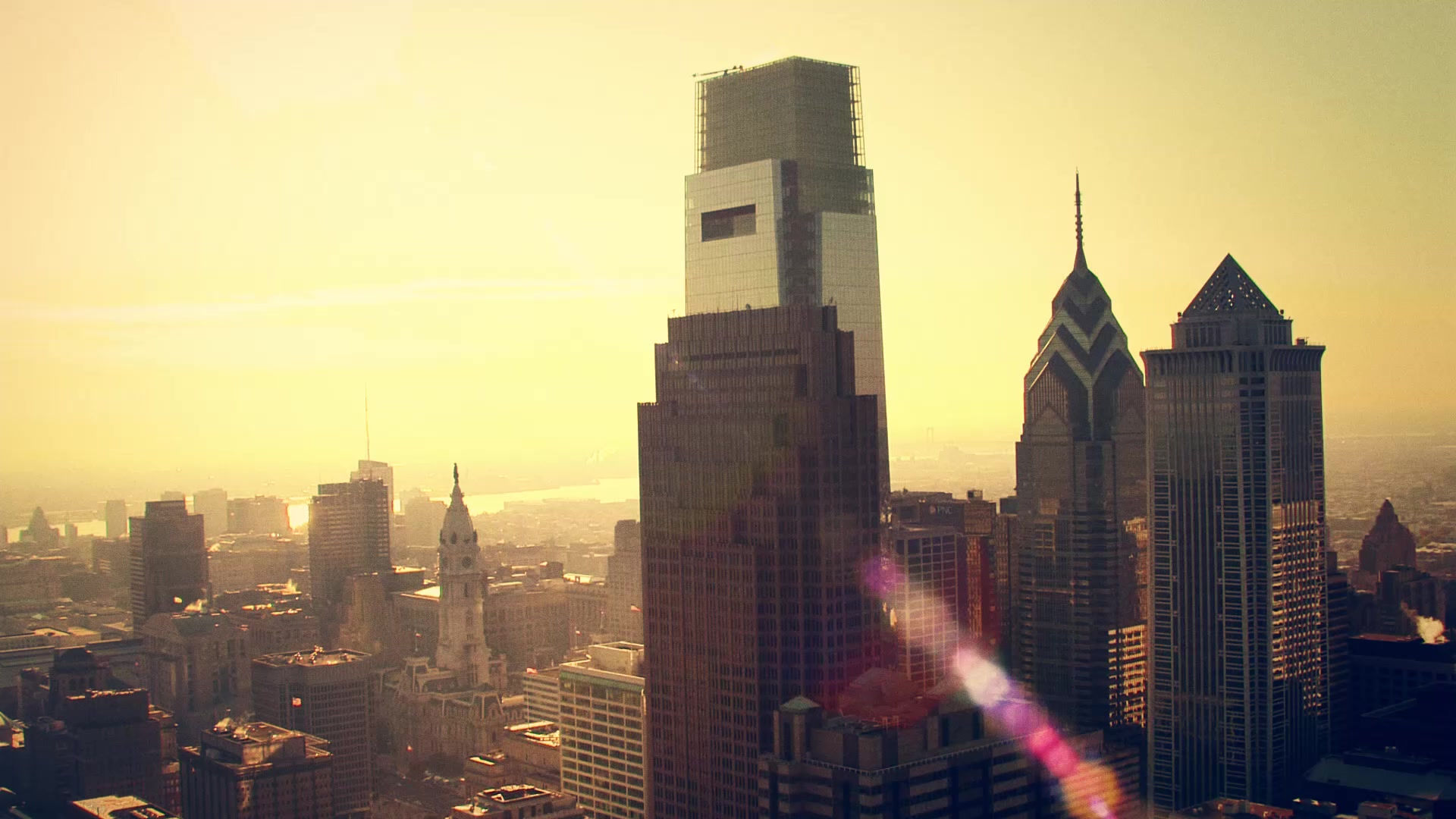

2024 Award Winners and Nominees
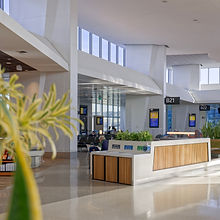
Project Name
SFO Harvey Milk Terminal 1 Boarding Area B

Description
San Francisco International Airport’s (SFO) 434,756 sq.ft. Harvey Milk Terminal 1 Boarding Area B (BAB) is a ground-up reconstruction project featuring 25 gates for domestic and international flights. BAB elevates travelers’ experiences with many retail and art installations, creating a galleria-like environment. The open gate lounges flow seamlessly with concessions, dining spaces and a special museum exhibit, all enhanced with work from local artists. A large children’s play area draws inspiration from regional landmarks and integrates with a central lounge at the end of the pier. A mezzanine houses airline clubs, a corridor to international connections and views of the concourse below. The design evokes the excitement of air travel while demonstrating SFO’s commitment to sustainability.
With the smart application of sustainable building practices and materials, this airport facility earned its designation as the world’s first certified LEED BD+C New Construction Platinum v4.0/4.1 terminal in 2022. With design beginning in 2015 and construction of the first phase completed in 2019, SFO’s Boarding Area B is among the first, if not THE first, project in the San Francisco Bay Area to introduce, and successfully deliver on, global warming potential limits in the concrete specifications.
The structure supporting this design is comprised of a deep concrete pile foundation and combination of concrete framing and lightweight concrete filled metal deck over steel columns and beams. Due to weak bay mud, the mat foundation had to be designed as a slab suspended between the concrete piles. The design also necessitated significant concrete shear walls for seismic loads. A total of ten different concrete mixes were specified for the various types of structural concrete elements through-out the project. Due to careful tuning of each mix through collaboration between the supplier Central Concrete Supply Company, Webcor Concrete Builders, structural engineer Rutherford and Chekene, and sustainability consultant Arup, the project achieved close to 30% embodied carbon reduction of 8.5M kgCO2e in the concrete, compared to the US national benchmarks first published by NRMCA.
Evidence
The success of the project began with the Airport, already leading the aviation industry in sustainable design, continuing to push the boundaries of “net zero” through the use of the Airport’s Sustainable Planning, Design, and Construction Standards. These Standards established maximum embodied carbon requirements for building materials and products. SFO’s Terminal 1 sustainability project leads directed the team to pursue the LEEDv4 materials credits when LEED version 4 had at the time of project inception only recently been introduced, and to achieve a design with lower embodied carbon when most confined the definition of “low carbon” to operational carbon only. Further enabling project achievement was the progressive Design-Build framework that allowed the sustainability consultant to initiate conversations between Webcor Concrete’s supplier, Central Concrete Supply Company, very early in design to identify representative concrete mixes and set appropriate global warming potential limits in the structural specifications, which the project team had not previously done. In working through the many questions that arose and accounting for the needs of these various parties, the SFO Big Room, a large collaborative work space was set up near the Terminal 1 construction site, that provided the multi-disciplinary team a way to quickly work out solutions face-to-face.
BAB raised the bar on what a progressive Design-Build approach can achieve through a commitment to Structured Collaborative Partnering process. Together, the team and stakeholders functioned as a single, integrated entity to deliver one unified vision with maximum value for a transformed Terminal 1 facility. The project ultimately attained three (3) LEED points for building lifecycle impact reduction plus two (2) points for forty (40) environmental product declarations (EPDs), of which a quarter came from Central Concrete Supply Company’s product-specific concrete EPDs, within LEED BD+Cv4.0/4.1 for New Construction certification program.
A few years later, the method of setting GWP limits in specifications to achieve embodied carbon reduction on BAB became an important project precedent for stakeholder acceptance of the GWP limit methodology that formed the backbone of the Marin County Low Carbon Concrete Code.
Images



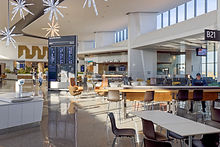

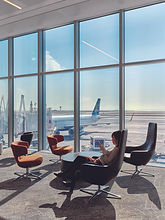

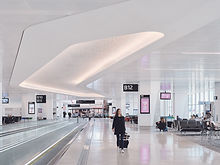

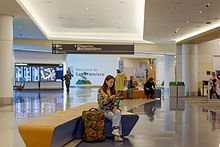
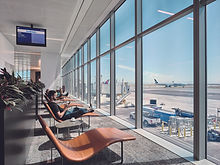
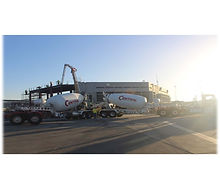